In the rapidly advancing field of industrial automation, the demand for more efficient and adaptable motor control systems has led to the development of the 860E Permanent Magnet Synchronous Frequency Converter. This cutting-edge system has been designed to offer precision, power, and versatility, making it an essential tool for industries requiring high-performance motor control solutions.
At the heart of the 860E Frequency Converter is its dedicated Digital Signal Processor (DSP) chip, which has been specifically optimized for motor control. This advanced chip provides robust current vector control capabilities, enabling the converter to deliver highly efficient and accurate motor drive control across various applications. Whether it is used in manufacturing, automotive, or HVAC systems, the 860E stands out for its ability to seamlessly manage both low and high torque demands.
Powerful and Reliable Performance
The 860E Permanent Magnet Synchronous Frequency Converter provides exceptional motor control, thanks to its intelligent DSP chip. This chip processes real-time data from the motor to optimize its performance, ensuring that torque and speed are finely tuned according to the operational requirements. The robust vector control capability allows for torque management and smooth speed regulation, even in highly demanding environments.
One of the key advantages of using the 860E is its adaptability to varying operational conditions. The converter supports a variety of frequency source superposition and switching methods, which enhances its flexibility and ensures it can perform optimally under different conditions. This adaptability is crucial in industries where motor load and operating environments can change frequently, such as material handling, pumps, and conveyor systems.
Enhanced Control Modes for Precision and Efficiency
The 860E Frequency Converter offers a variety of control modes to suit different motor types and applications, making it a versatile tool for various industries. Among the three primary speed control methods are Sensorless Vector Control (SVC), V/F Control (Voltage/Frequency Control), and closed-loop vector control. These modes provide users with a range of options for controlling motor performance depending on the application and its specific requirements.
The SVC mode is particularly noteworthy because it can achieve a starting torque of 150% at just 0.5Hz, which is essential for applications that demand strong and immediate starting forces. For example, machinery that requires high torque to start up, such as crushers, mixers, or hoists, will greatly benefit from this feature. The ability to deliver such high starting torque ensures that the system operates smoothly from the start, avoiding unnecessary delays and mechanical strain.
The V/F control mode, on the other hand, is a simpler but effective method of motor control, typically used in applications where precision is less critical. It offers a straightforward way to manage motor speed, making it an ideal choice for fans, pumps, and other applications where consistent but not exact speed control is sufficient. This mode is also highly energy-efficient, which can lead to cost savings in industries with extensive motor usage.
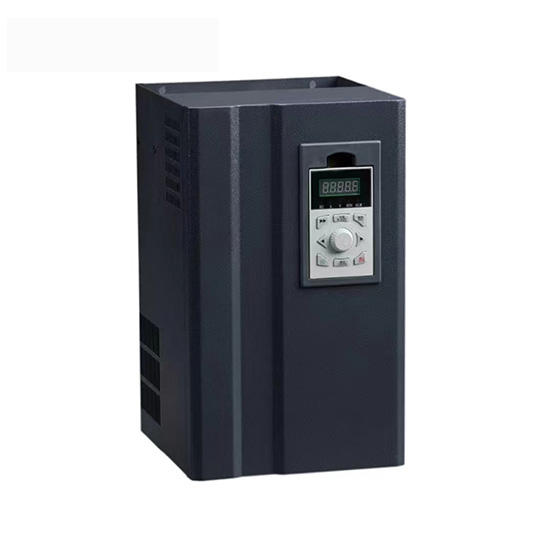
For more demanding applications, the closed-loop vector control method provides the level of performance by incorporating feedback from the motor. This method allows the frequency converter to continuously adjust motor parameters in real-time to maintain performance. It is especially useful for applications that require both precision and flexibility, such as robotics, CNC machinery, or complex material processing systems.
Overload Capacity for High-Demand Applications
The 860E Frequency Converter is built with industrial resilience in mind. It features an overload capacity of 150% for up to one minute, ensuring that the system can withstand short-term spikes in load without compromising on performance. This feature is particularly valuable in high-demand applications where machinery is subjected to sudden increases in load or torque, such as in production lines, presses, and heavy-duty machinery. The ability to manage these overload conditions without failure ensures continuous operation, reducing downtime and increasing overall productivity.
This overload capacity is a key aspect of the 860E’s reliability, making it an attractive choice for industries that operate under fluctuating or unpredictable conditions. The converter’s ability to handle brief overloads without risk of damage helps extend the life of both the frequency converter and the motor, to reduced maintenance costs and greater long-term savings.