In industrial settings, starting large motors can often lead to significant challenges. These motors, which power everything from heavy machinery to large pumps and compressors, require an effective and reliable method for starting up without causing harm to the equipment. A common problem is the initial inrush of current that occurs when the motor is powered on, which can damage the motor, reduce its lifespan, and put strain on the entire electrical system. Enter the autotransformer reduced-voltage starter cabinet—a technology designed to address these challenges by providing a smoother, more controlled startup process, ensuring both the longevity of the motor and the efficiency of the electrical system.
Efficient Voltage Reduction: A Smoother Startup
One of the core benefits of the autotransformer reduced-voltage starter cabinet is its ability to efficiently reduce the voltage during motor startup. When a motor is powered on, the sudden rush of electricity to the motor can cause an initial spike in current, known as the "inrush current." This surge can be as much as five to seven times the motor's normal running current, putting significant stress on the motor windings and potentially causing damage to the motor over time.
By using an autotransformer to reduce the voltage during startup, the current is also reduced in proportion. This reduction in voltage helps to mitigate the damaging effects of high inrush current. Instead of a sudden surge, the motor starts up more gradually, reducing the mechanical stress on the motor's components and allowing for a smoother transition to normal operation. This smoother startup process not only protects the motor but also helps to maintain the integrity of other equipment connected to the system, preventing potential damage from the initial surge.
Cost-Effective: Lower Electrical Costs and Fewer Interruptions
Aside from protecting equipment, the reduced inrush current facilitated by the autotransformer starter cabinet brings additional financial benefits. One of the main advantages is the reduction in stress on the power supply network. When a large motor is started with a high inrush current, it can cause a temporary dip in voltage in the power supply, to fluctuations that can affect other machinery or systems connected to the grid.
With the autotransformer system, however, this voltage dip is minimized, which reduces the likelihood of power interruptions or the need for additional grid stabilization measures. As a result, businesses can enjoy a more stable electrical supply without worrying about potential interruptions that could lead to costly downtime or damage to sensitive equipment.
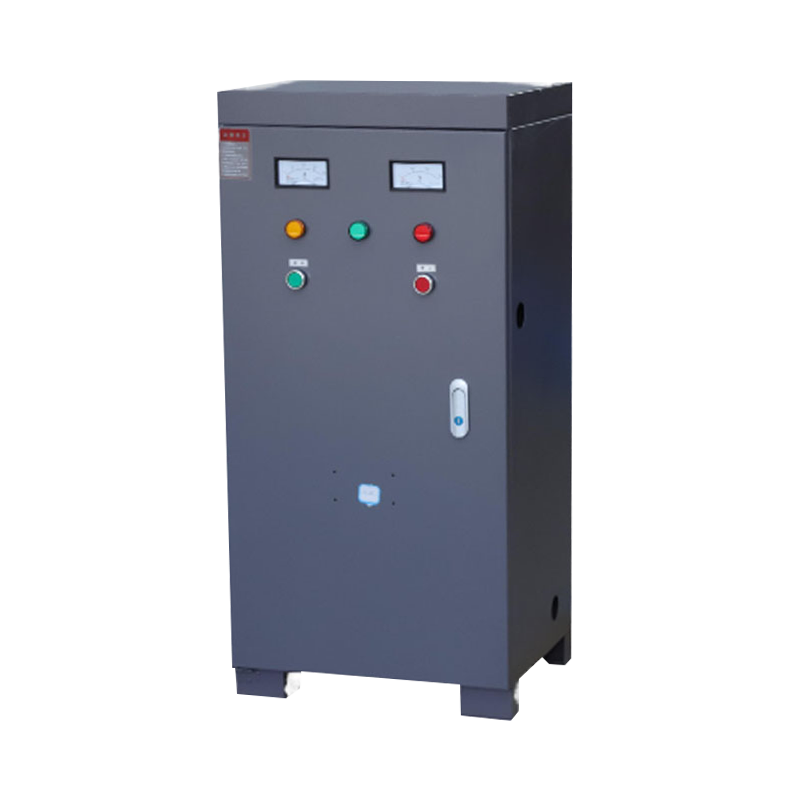
Additionally, by reducing the inrush current, the autotransformer starter cabinet can lower overall energy costs. With traditional direct-on-line (DOL) motor starting methods, the high inrush current means that the system draws significantly more power in the initial moments of startup. Over time, this can add up to substantial energy costs. By reducing the power required during startup, the autotransformer system helps minimize these additional charges, making it a cost-effective solution for industries looking to optimize their energy consumption.
Moreover, the reduced inrush current also has a positive impact on the longevity of the motor itself. Motors that are subjected to frequent high inrush currents experience more wear and tear on both their electrical and mechanical components. The autotransformer design helps minimize this stress, ultimately to fewer repairs, longer service life, and a lower total cost of ownership for businesses that rely on heavy machinery.
Enhanced Durability: Built to Last in Tough Environments
In industrial applications, equipment is often exposed to harsh conditions, from temperatures to high levels of humidity, dust, and vibration. For a motor starter system to be reliable, it must be able to withstand these environmental factors without compromising performance. The autotransformer reduced-voltage starter cabinet is built with durability in mind, ensuring that it can handle the challenges of tough industrial environments.
The cabinet's robust shell is specifically designed to protect the components inside from physical damage and environmental stresses. Whether it's exposed to corrosive chemicals, excessive heat, or moisture, the cabinet is constructed to keep the internal components secure and protected. This durability is crucial in maintaining a reliable system that won't fail unexpectedly, particularly in industries where equipment downtime can result in significant financial losses.