In the modern industrial landscape, precision and efficiency are at the forefront of technological advancement. One of the key innovations driving this progress is the high-performance vector inverter. These sophisticated frequency converters have transformed motor control systems, enhancing productivity across numerous industries, from manufacturing to energy management.
The Power of Vector Control Technology
A vector inverter operates on the principle of field-oriented control (FOC), which allows for precise manipulation of an asynchronous motor’s speed and torque. Unlike traditional voltage-frequency (V/F) control, vector control dynamically adjusts the motor’s magnetic flux and torque-producing current, delivering responsiveness and energy efficiency.
High-performance vector inverters incorporate specialized digital signal processors (DSPs) to execute real-time calculations, ensuring accuracy in speed regulation and load adaptability. This level of control is crucial in applications requiring high torque at low speeds, such as in conveyor systems, textile machinery, and automated production lines.
Enhancing Efficiency in Industrial Applications
Industries worldwide are seeking solutions to reduce energy consumption and enhance machine lifespan. A well-designed vector inverter achieves this by optimizing motor performance based on real-time load conditions. The ability to maintain torque under varying loads makes it particularly effective in applications such as:
Textile and Paper Industry – Precise speed regulation prevents material wastage and ensures uniform quality.
Food and Packaging Sector – Consistent motor control is vital for automated filling, sealing, and cutting machines.
Ventilation and Pump Systems – Energy-efficient control of fans and pumps leads to significant power savings.
Heavy Machinery and Automation – Smooth acceleration and deceleration reduce mechanical stress on components.
The integration of high-performance vector inverters into these systems not only improves operational efficiency but also extends the life of industrial equipment by minimizing unnecessary wear and tear.
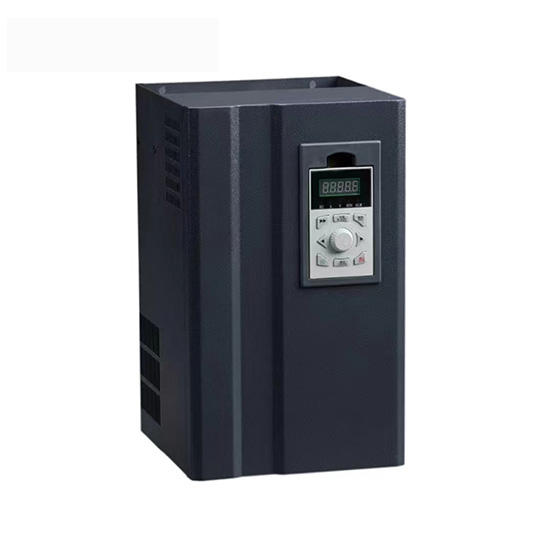
Advanced Features for Modern Industry
The latest generation of vector inverters comes with an array of advanced features designed to meet the diverse demands of various industries. Some of the notable functionalities include:
Multi-Speed Operation – Allows for the programming of different speed levels to match production requirements.
Adaptive PID Control – Enhances process stability by adjusting motor response based on real-time feedback.
Frequency Source Customization – Offers flexibility in controlling motor speed through different input methods.
Speed Tracking and Auto-Tuning – Enables smooth restarts and performance adjustments based on system needs.
Comprehensive Safety Protections – Includes overcurrent, overvoltage, and thermal protection to ensure operational safety.
These intelligent capabilities make high-performance vector inverters indispensable for modern industrial automation, where reliability and adaptability are key.
The Impact on Smart Manufacturing
As industries embrace the era of smart manufacturing, vector inverters play a critical role in enabling seamless integration with digital automation systems. Many advanced inverters now support communication protocols such as Modbus, CANopen, and EtherCAT, allowing for real-time data exchange and remote monitoring. This connectivity enhances predictive maintenance strategies, reducing unplanned downtime and optimizing resource utilization.
Moreover, the compatibility of vector inverters with Internet of Things (IoT) frameworks enables operators to monitor performance metrics, analyze energy consumption trends, and implement data-driven optimizations. The result is a smarter, more sustainable industrial environment.
Meeting Global Standards and Sustainability Goals
With growing regulatory emphasis on energy efficiency and environmental sustainability, industries are under pressure to adopt eco-friendly technologies. High-performance vector inverters contribute to these goals by minimizing power wastage and optimizing motor efficiency. Their compliance with international standards ensures that manufacturers can meet regulatory requirements while achieving cost savings through reduced energy consumption.
Furthermore, the reduced mechanical stress facilitated by vector-controlled motor operation leads to lower maintenance costs and less frequent equipment replacement, promoting a more sustainable approach to industrial automation.