In the ever-evolving world of industrial automation and motor control, frequency converters play a pivotal role in ensuring machines operate efficiently and effectively. One of the standout solutions in this space is the newly developed 860D High Protection Frequency Converter, which has taken performance to the next level with its advanced speed control and versatility.
Frequency converters are essential components in a wide variety of industries, from manufacturing to HVAC systems, as they regulate the speed of electric motors, reduce energy consumption, and improve operational precision. The 860D High Protection Frequency Converter comes equipped with a host of features that make it a option for industries that require reliability and precise control.
Multiple Control Methods for Greater Flexibility
One of the primary features that set the 860D apart is its multi-mode speed control capabilities. The device supports three distinct speed control methods: Sensorless Vector Control (SVC), V/F control, and closed-loop vector control. These control methods allow users to tailor the frequency converter’s operation to different motor types and operational needs.
The Sensorless Vector Control (SVC) mode, in particular, offers exceptional performance for motors requiring high torque at low speeds. This mode is ideal for applications that demand precision, such as conveyor systems or pumps. It can deliver an impressive starting torque of up to 150% at just 0.5Hz, ensuring smooth and efficient starts without straining the motor. The SVC mode also maintains torque stability, even at low speeds, making it for processes that require constant adjustments.
In addition to SVC, the V/F control (Voltage/Frequency control) method offers a simpler, more cost-effective solution for applications where precise control over motor speed isn’t as critical. It is a commonly used method in applications such as fans and water pumps, where a standard motor speed variation is sufficient.
Lastly, the closed-loop vector control method integrates feedback from the motor to optimize its performance. This provides the level of control and efficiency, making it the go-to choice for high-performance applications that require precise speed regulation and torque management.
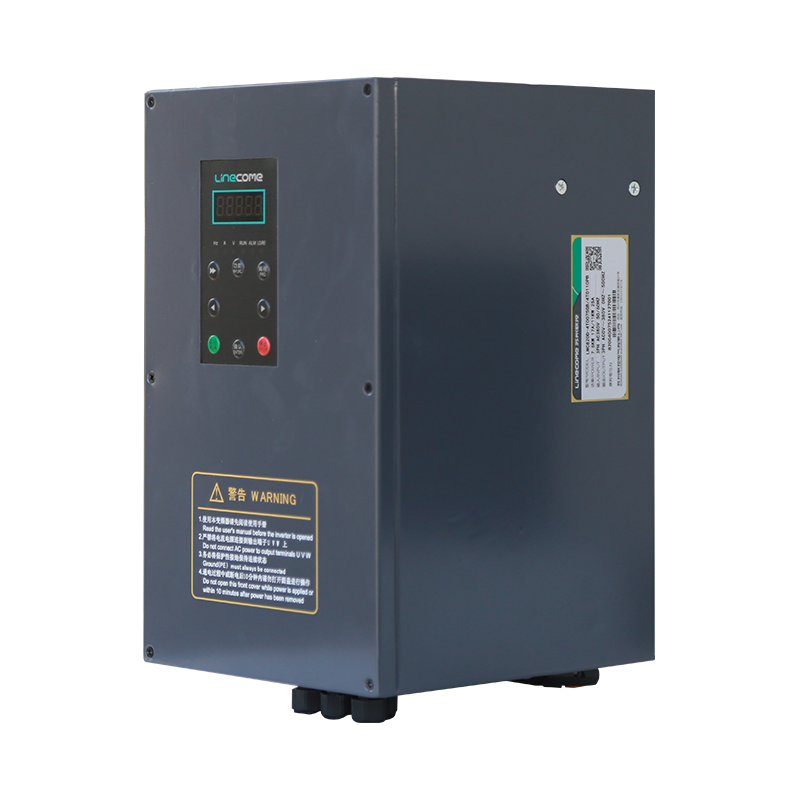
Overload Capacity for High-Demand Applications
The 860D High Protection Frequency Converter is also designed to handle challenging operational environments with ease. It boasts an impressive overload capacity of 150% for up to one minute, which ensures the device continues to operate under demanding conditions without compromising on performance or reliability. This feature is particularly beneficial in industries where peak loads are common, such as manufacturing, packaging, or material handling, as it guarantees that the system remains operational even during short-term spikes in demand.
This overload capability ensures that the 860D can manage unexpected surges in power or fluctuations in load, providing users with peace of mind that their operations will continue smoothly without disruption.
Extensive Control Options
Beyond its advanced speed control methods, the 860D High Protection Frequency Converter offers an array of flexible control options to suit a wide range of industrial applications. With 16-segment speeds, users can program and adjust the converter to meet specific speed requirements for various stages of their processes. This feature is especially useful in industries like automotive manufacturing, where different phases of production might require different motor speeds.
The converter also supports automatic program operation, which allows it to automatically transition between different speed settings or operational modes based on preset conditions. This capability is ideal for applications where processes need to be automated or where constant monitoring and adjustments are necessary to ensure performance.
The 860D allows users to set the frequency through multiple methods, ensuring compatibility with various systems and operational requirements. These settings include digital setting, analog setting, PID setting, and multi-segment speed setting. These options give users full control over the motor’s behavior, making it easy to fine-tune the system for efficiency.
For users requiring even more customization, the simple PLC setting enables integration with programmable logic controllers for more complex automation processes. In addition, the PULSE pulse setting and RS485 communication setting provide further flexibility for users in need of precise control or remote communication capabilities. Whether you are managing a single motor or a network of interconnected systems, the 860D's communication options make it easier to integrate the frequency converter into existing setups.