As industries across the globe strive to optimize their operations, the demand for versatile, cost-effective, and high-performance motor control systems has never been greater. One such innovation that has gained significant traction is the Single Module General-Purpose Inverter. Designed to meet the diverse needs of modern industrial applications, these inverters provide enhanced flexibility, performance, and an efficient means of controlling motor-driven equipment.
Inverters, often referred to as frequency converters, are integral to the efficient operation of electric motors. They regulate the speed, torque, and performance of motors by controlling the frequency and voltage of the electrical supply. For many industries, having the ability to tailor motor performance to meet specific needs is essential to achieving results. The Single Module General-Purpose Inverter, particularly the 500 Series Frequency Converter, offers an array of features that make it an ideal solution for businesses seeking precision and efficiency in their operations.
Wide Output Frequency Range: Meeting the Needs of a Diverse Range of Industries
One of the standout features of the Single Module General-Purpose Inverter is its wide output frequency range, making it suitable for a broad spectrum of industrial applications. The 500 Series Frequency Converter offers an impressive output frequency range of 0–500Hz, a range that is more than adequate for industrial processes, including conveyor systems, pump operations, HVAC systems, and general machinery.
For industries with more specific or specialized needs, the inverter can be further customized to support an extended frequency range of 0–3000Hz. This flexibility opens up new possibilities for high-performance applications such as high-speed machining, precise testing equipment, and other high-frequency operations that require advanced control. Industries such as textiles, electronics, and automotive manufacturing, where equipment must operate at high speeds or with high precision, can now rely on the 500 Series Frequency Converter to provide a customized solution for their motor control needs.
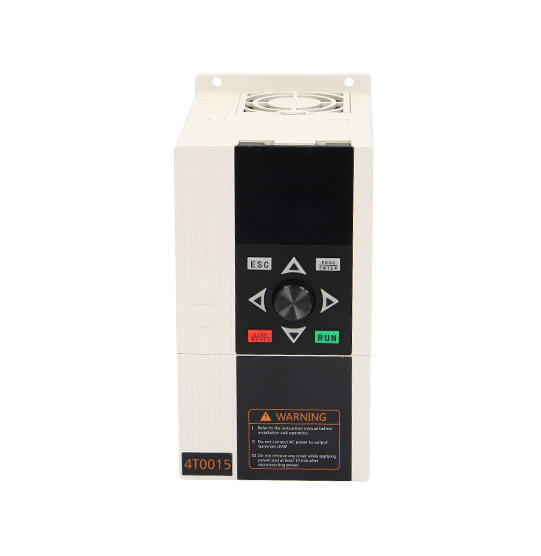
The ability to adjust the output frequency to match specific operational requirements enhances the adaptability of this inverter, allowing it to support a wider variety of applications while ensuring that the machinery operates at peak efficiency.
Advanced Speed Control Methods: Tailored for Motor Performance
A key factor that sets the Single Module General-Purpose Inverter apart from its competitors is its versatile speed control capabilities. The 500 Series Frequency Converter is equipped with three distinct speed control methods, each designed to offer varying levels of precision and performance, depending on the requirements of the application.
Sensorless Vector Control (SVC): This method is particularly beneficial for applications that require high torque at low speeds. Sensorless Vector Control provides impressive starting torque—up to 150% of the rated torque—at as low as 0.5Hz. This makes it an ideal choice for operations that demand reliable low-speed performance during startup, such as conveyors, crushers, and fans. The SVC method ensures smooth, consistent operation even under challenging load conditions, minimizing the risk of mechanical wear and providing motor control at all speeds.
V/F Control (Volts per Frequency Control): Often used in more standard applications, V/F control offers a simple and effective way to regulate motor speed. By maintaining a constant ratio of voltage to frequency, V/F control ensures stable motor operation, even in less demanding processes. It strikes a balance between simplicity and performance, making it an excellent option for applications such as ventilation systems, pumps, and basic conveyors. The method is particularly advantageous for processes that do not require precise speed adjustments but still demand consistent motor performance over time.
Closed-loop Vector Control: This advanced control method provides the level of performance and precision. Closed-loop Vector Control continuously monitors the motor’s speed and torque, adjusting the frequency and voltage in real-time to ensure efficiency. This method is particularly useful for complex industrial systems that require high precision and consistent operation under varying load conditions, such as CNC machines, robotics, and automated manufacturing lines. Closed-loop Vector Control offers a level of responsiveness that ensures the motor performs with minimal energy waste and efficiency, making it ideal for applications where performance is critical.