As industries strive for greater efficiency, precision, and adaptability in motor control, vector inverter technology has emerged as a game-changer. These advanced frequency converters provide exceptional speed regulation, high torque performance, and robust overload capabilities, making them indispensable in a wide range of industrial applications. From manufacturing and automation to HVAC and high-speed machining, vector inverters deliver the precision and reliability needed to meet modern operational demands.
Expanding Operational Flexibility with a Wide Frequency Range
One of the key advantages of vector inverters is their broad frequency range, which typically extends from 0 to 500Hz. Some advanced models can even reach up to 3000Hz, catering to industries that require precision and high-speed operation.
This extensive frequency range allows vector inverters to support diverse applications, including:
CNC machining, where ultra-high-speed spindle motors demand precise frequency control.
Textile manufacturing, where varying fabric densities require adaptable motor speeds.
Food processing, where conveyor belt speeds must be fine-tuned for different production stages.
By enabling such precise frequency adjustments, vector inverters optimize performance across industries, ensuring efficiency and output quality.
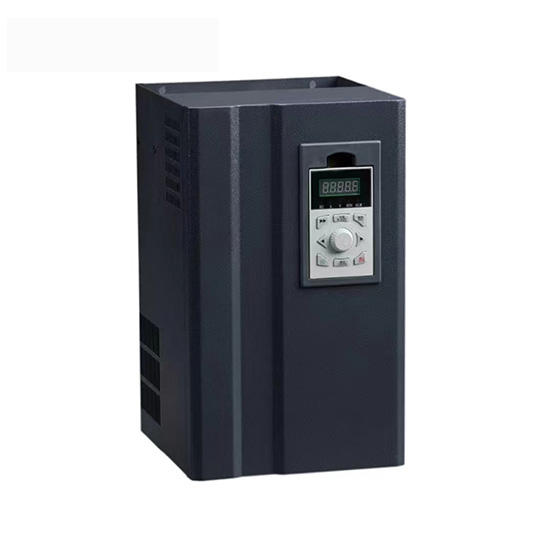
Advanced Speed Control for Dynamic Performance
Modern vector inverters offer multiple speed control modes to accommodate different operational needs. The three common modes include:
Sensorless Vector Control (SVC) – This mode provides enhanced torque and speed control without requiring an external feedback device. It enables a starting torque of 150% at 0.5Hz, making it ideal for applications that require strong startup power, such as heavy-duty conveyors and cranes.
V/F Control (Voltage/Frequency Control) – A more traditional method used for applications that do not require precise torque regulation but still need smooth acceleration and deceleration. This is commonly applied in pumps, fans, and HVAC systems.
Closed-Loop Vector Control – The precise mode, utilizing feedback sensors to adjust speed and torque dynamically. This is essential for robotic automation, high-precision machining, and positioning systems where accuracy is critical.
With these versatile control options, industries can fine-tune motor performance according to their specific application requirements, achieving both energy efficiency and output.
Robust Overload Capacity for Demanding Applications
Industrial environments often present unpredictable load variations that can strain motor performance. Vector inverters address this challenge with their strong overload capability, which can handle up to 150% of rated load for up to one minute.
This feature ensures operational stability in high-demand settings such as:
Material handling systems, where sudden load changes occur due to varying weights.
Mining equipment, where motors frequently experience heavy resistance.
Steel and metal processing, where machines must endure conditions.
By preventing system failures and reducing downtime, vector inverters enhance productivity and extend the lifespan of industrial motors, making them a cost-effective investment for businesses.
Energy Efficiency and Cost Savings
With rising energy costs and increasing environmental regulations, industries are seeking solutions that reduce power consumption while maintaining high performance. Vector inverters contribute to this goal by optimizing motor speed and torque based on real-time demand.
Key energy-saving benefits include:
Reducing inrush current at startup, preventing energy spikes.
Eliminating unnecessary power usage by adjusting motor speed dynamically.
Enhancing regenerative braking efficiency, which recycles excess energy back into the system.
Industries that integrate vector inverter technology can significantly lower their electricity bills and minimize their carbon footprint, making them more sustainable in the long run.
Industry Applications: Where Vector Inverters Make an Impact
Vector inverters have become essential in numerous sectors, offering unparalleled performance in motor control. Some key industries benefiting from this technology include:
1. Manufacturing and Automation
Precision control is crucial in assembly lines, robotic systems, and automated machinery. Vector inverters ensure smooth motion control, minimal vibration, and high-speed accuracy, to faster production cycles and improved product quality.
2. HVAC and Pumping Systems
In air conditioning, ventilation, and water treatment plants, energy-efficient operation is a top priority. Vector inverters dynamically adjust fan and pump speeds, reducing power consumption without compromising performance.